寧波公牛電器有限公司為公牛集團下屬子公司,成立于2007年,經過8年發(fā)展到2015年成為亞洲最大的墻壁開關生產基地,中國市場市占率第一,10戶中國家庭,7戶用公牛?!坝貌粔摹笔枪Ξa品質量的詮釋,也是用戶選擇公牛的理由。2022年市場產品不良率154ppm,中國市場質量第一,成為新的行業(yè)標桿,質量如何保證5億只產品的可靠性水平達到行業(yè)標桿,公牛從2019年開始踐行自主質量管理方法論,這套方法論2022年入圍“工信部全國制造業(yè)可靠性提升優(yōu)秀案例”。2023年4月3日發(fā)布的《2022胡潤品牌榜》公牛以195億元的品牌價值第一名領銜寧波企業(yè)。
公牛在創(chuàng)立之初,便把“用不壞的插座”作為產品設計的基本理念,充分考慮客戶使用場景,制定高于國家要求的嚴苛企業(yè)標準,在結構、工藝、材料設計均走在行業(yè)前列,設計上預留冗余,從源頭保證產品質量,助力寧波公牛登頂市占率第一。但是,市占率第一,外部質量不良率卻只有659ppm,距離行業(yè)標桿164ppm
還有很大的差距。不禁思考,僅僅依靠設計冗余就足夠了嗎?在制造業(yè),人、機、料、法、環(huán)以及不可控的因素造成的過程變差是不可避免的,它會影響產品的質量波動,造成生產出的產品質量參差不齊或不符合設計要求。所以,控制過程變差變得尤為重要。
為此,公司質量提升向控制過程變量轉變,結合了自主質量的技術平臺,創(chuàng)造性提出自主質量的概念。通過控制設計變差、過程變差、供應鏈變差來提升產品質量可靠性。孵化出設計端可靠性評價,可信供應鏈,工廠端以防產生、防流出、問題根本解、標準化作業(yè)為四個維度的標桿線,輔助產線自主質量管理的數(shù)字化管理平臺等四大子項目,同時制定Q績效牽引,推動實現(xiàn)力公司生產高可靠性,高性價比產品的質量愿景。
控制過程可控變差可在很大程度上提升產品的可靠性,使得外部不良率呈倍數(shù)級下降,但過程的不可控因素依然存在,且無法管控,由這些不可控因素造成的產品問題依然有待解決。為此,我們重新識別了質量核心職責---“多發(fā)現(xiàn)問題,多做根本解”,提出所有人需正視問題,并將問題當做機會,建立負面問題清單,拉通全流程推行以“優(yōu)化設計”“升級設計標準”“優(yōu)化工藝—增加防呆”“優(yōu)化工藝—增加100%自動測試”為解決措施的問題根本解方法,并通過指標牽引輻射到所有部門,真正實現(xiàn)全員質量。
在質量成本方面,自主質量與根本解可助力實現(xiàn)質量免費,通過可靠性評價、標桿線打造、可信供應鏈、質量自主管理平臺、Q績效幫助產線提升標桿線星級得分,達到一定的得分后,可實現(xiàn)無人檢驗,完全由產線進行自主質量管理,降低人力成本的同時提高產品質量可靠性。
在可推廣性方面,自主質量與根本解具有完整的邏輯,借用研發(fā)和自主質量的技術平臺來實現(xiàn),改變了傳統(tǒng)的質量管理模式:由控制產品規(guī)格變?yōu)榭刂飘a品可靠性。具備行業(yè)創(chuàng)新性,并可對方法論進行推廣,目前自主質量已在公牛集團內部平行推廣,可推廣性高,可助力行業(yè)質量管理革新。
案例背景:近年來,墻開市場容量下降了13%,在市場負增長的環(huán)境下,存量競爭將變得越來越激烈,同時墻開產品毛利率逐年下降,從這里我們識別到,極致性價比的質量領先將為存量競爭構建富有競爭力的護城河。那么質量領先就將作為質量的發(fā)展戰(zhàn)略,其中包含兩層含義,第一是不良率第一,第二是一致性第一。首先是不良率方面,從寧波公牛三年的質量表現(xiàn)看,外部不良下降了76%。是國際行業(yè)標桿的0.94倍,已成為行業(yè)天花板。再來看下質量領先之一致性的背景,首先解釋下什么是一致性,一致性意味著制造的產品與設計保持一致的程度,也意味著產品與產品之間保持一致的程度。基于此,我們對比了我司產品與行業(yè)標桿的產品壽命特性,發(fā)現(xiàn)我司產品壽命性能浮動較大,與標桿尚存在一定的差距,從統(tǒng)計學上來說,我們屬于矮胖型,標桿屬于精瘦型,這是我們的挑戰(zhàn),同時也把它看做是提升品牌力的一次機會,所以怎么提高產品性能的一致性,對質量模型進行瘦身,成為了需要解決的問題。實現(xiàn)產品質量一致性提升,僅依靠設計冗余來保證是不夠的,還需要借助技術手段控制過程變差,保證不良品不被生產,生產了不被流出。由此部署自主質量作為質量戰(zhàn)略項目,并參考經濟學里的洛倫茲曲線創(chuàng)造性提出質量一致性指數(shù)概念(產品設計時各個零件性能保持一致及生產制造出來的產品其關鍵質量特性與設計目標保持一致的程度),作為自主質量的主要實施目標。
同時,過程的不可控因素依然存在,難以通過自主質量控制,由這些不可控因素造成的產品問題依然有待解決,故此需要全流程推動負面問題根本解。
案例詳情:公司提出自主質量作為公司的質量戰(zhàn)略項目,從客戶角度出發(fā),識別出股東、研發(fā)、工業(yè)化、工廠、供應商、顧客六大相關方,并識別其對質量的需求,從股東的“質量好,有利潤,零浪費”到顧客的“花相同的錢,享受更多的產品價值”端到端的需求閉環(huán)。研發(fā)承接股東的需求,在產品設計之初識別產品關鍵特性,并將其拆解為組件與零件特性,通過可靠性評價模型找到設計平衡點,并對影響特性的點進行防呆防錯設計。工業(yè)化承接研發(fā)的設計輸出,利用QFD工具將其轉化為工程語言加以控制,引入CLE生產制程能力評價工具(L1代表利用了防呆防錯技術,消除缺陷發(fā)生的機會;L2代表利用早起預警系統(tǒng)防止不良品流出,例如SPC工具;L3代表工序可靠性依靠操作者,依賴文件、培訓和工具探查缺陷發(fā)生;L4代表工序無質量控制計劃,容易產生缺陷)對生產線的每到工序進行能力評價,由此產生產線的工藝改善清單,來保證工藝方面不產生不流出不良品。工廠承接自主質量輸出的工藝標準,全面打造質量標桿線,在業(yè)內創(chuàng)造性的將“特殊特性的識別、傳遞與管控”的制造業(yè)屬性與“用戶思維,信息交互,自主管理”的互聯(lián)網思維相結合,將傳統(tǒng)的依靠質量部的質量管理轉變?yōu)橹圃熳灾髻|量管理,基于生產MES系統(tǒng)開發(fā)自主質量管理平臺,參考美團、滴滴等互聯(lián)網平臺邏輯,將生產線體當做店鋪,在防產生、防流出、問題根本解、標準化作業(yè)四個維度設定一定的規(guī)則,四個維度綜合得分為“店鋪”的標桿線星級得分,線長為“店鋪”的老板,可以驅動各改善人員在四個維度上做相應對策
提升“店鋪”星級。除此之外,建立一套Q績效規(guī)則來激勵員工向更高的得分邁進。供應商承接研發(fā)的零件設計輸出,在供應商端推行可信供應鏈,開發(fā)供應商管理平臺,其管理邏輯與工廠的質量自主管理平臺類似,借此助力供應商提高零件質量可靠性。結合可信供應鏈所提供的高可靠性零件與工廠生產質量自主管理平臺,產線可持續(xù)穩(wěn)定的輸出高可靠性產品至顧客端,顧客在接收到產品后可享受到高性價比高可靠性的又好又便宜的產品,愿意為其買單并愿意推廣,由此實現(xiàn)股東的“質量好,有利潤,零浪費”需求,實現(xiàn)端到端的需求閉環(huán)。
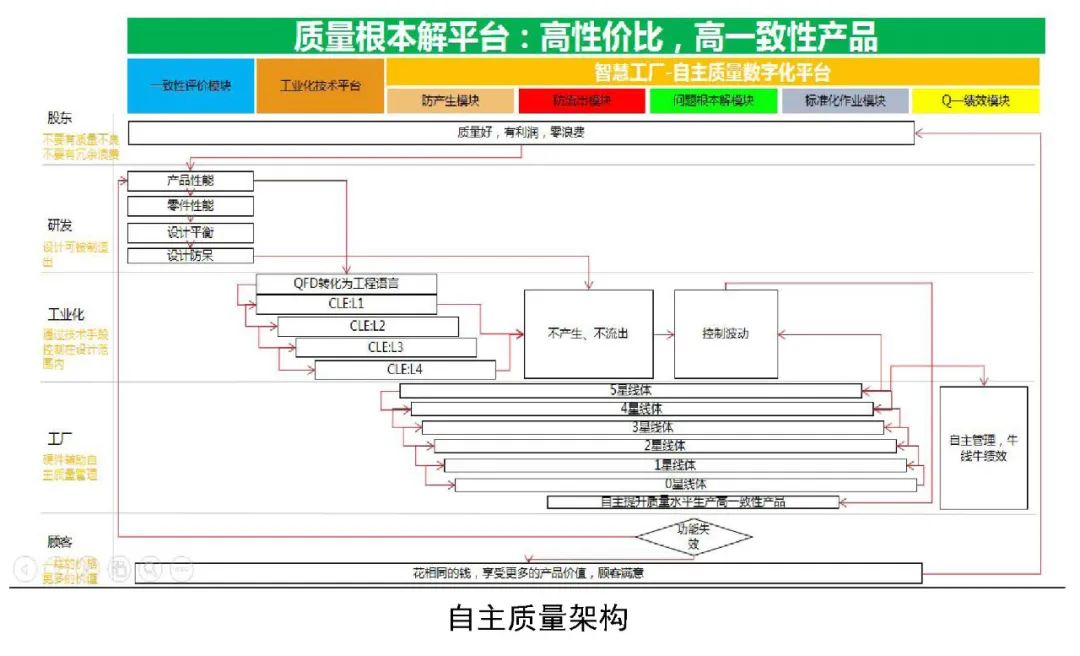
技術上推行自主質量,管理上提出將問題當做改善機會,重新建立質量管理流程,以問題到根本解貫穿客戶質量、新品質量、過程質量、供應商質量、實驗室、成品檢驗、部件檢驗七大質量模塊流程,并總結出質量流程革新五步法:
第一步,識別核心職責。重新梳理識別了部門核心職責為“早發(fā)現(xiàn)問題、多發(fā)現(xiàn)問題,聚焦根本解并”;
第二步,制定核心KPI。對核心KPI革新,檢驗員KPI為發(fā)現(xiàn)問題數(shù),工程師KPI為根本解關閉率,以此激勵所有人多發(fā)現(xiàn)問題,多推動根本解;
第三步,建立流程標準。以核心職責和KPI為基礎,建立負面問題清單管理流程,將問題發(fā)現(xiàn)邏輯與根本解管理邏輯納入其中,統(tǒng)一問題清單,將碎片化信息歸一化;
第四步,建立DM管理機制。建立微信群、周會、日會等不同形式點檢機制,每天點檢負面問題清單,從事業(yè)部層級到質量部、各流程部門層級,再到下屬各模塊,分層級日點檢,確保問題被跟進,閉環(huán);
第五步,建立績效考核規(guī)則。革新檢驗員與工程師績效考核規(guī)則,以月度/季度點檢指標考核,并將所有人的指標每日動態(tài)公示,激勵員工向高目標挑戰(zhàn)。同時將根本解關閉率作為質量以及各相關部門的流程指標,牽引各部門多做根本解。
應用場景:自主質量在公司內外部都有應用,內部主要在研發(fā)端、工業(yè)化端、工廠端實施,外部主要在關鍵供應商端實施。
自主質量推進分為三個大步驟,第一步主要搭建自主質量基礎框架,包括工具方法的引入、流程的優(yōu)化、信息化平臺的搭建等;第二步在基礎框架下,內外部持續(xù)推行自主質量落地成效,覆蓋內部產線與外部供應商。第三步,在一定基礎的供應鏈與內部質量水平下,推行無人檢產線,真正做到質量自主管理,降低質量成本,持續(xù)提高質量水平,并形成方法論向內外推廣,助力“10戶中國家庭,7戶用公牛的”第一品牌。
申報獎項:本項目在公司內部獲得集團制造技術科技成果獎,外部獲得了慈溪市經信局專項激勵,入圍了工信部科技司&電子第五研究所《全國制造業(yè)可靠性提升優(yōu)秀案例》,取得了各大權威部門的認可。
創(chuàng)新性、代表性經驗:自主質量管理模式在集團內部、墻壁開關行業(yè)甚至制造業(yè),自主質量數(shù)字化管理屬于行業(yè)首創(chuàng),其邏輯清晰,可復制性強。
技術方面,創(chuàng)造性提出自主質量的概念,在研發(fā)、工業(yè)化、工廠、供應商四個方面發(fā)力,從設計到零件到工藝最后到成品生產,全流程推行自主質量概念,并開發(fā)信息化平臺,輔助生產和供應商進行質量管理,質量人員制定管理規(guī)則,為自主質量管理建造高速公路,由此質量人的價值由檢驗質量逐漸轉變?yōu)樾畔⒒脚_運維質量,輔助工廠將年產5億只的“巨無霸”,逐漸武裝成能在“高速公路”上快速奔跑的“裝甲車”!
管理方面,不同于傳統(tǒng)質量管理方式,懼怕問題,創(chuàng)新性提出“問題=改善機會”的質量邏輯,建立負面問題清單,擁抱問題,并鼓勵多發(fā)現(xiàn)問題,對檢驗員進行績效革新,唯一績效為發(fā)現(xiàn)問題數(shù),以此激勵所有人員多發(fā)現(xiàn)問題,并多發(fā)現(xiàn)高含金量問題。然后將問題變?yōu)楦纳茩C會,所有工程師負責推動以“優(yōu)化設計”“升級設計標準”“優(yōu)化工藝—增加防呆”“優(yōu)化工藝—增加100%自動測試”為解決措施的問題根本解方法,同時將根本解關閉率作為質量以及各相關部門的流程指標,牽引所有人多做根本解。
應用成效:通過推行自主質量與“多發(fā)現(xiàn)問題,多推動根本解”的質量革新流程,取得了以下效果:
◆建立了全員“多發(fā)現(xiàn)問題,多推動根本解”的質量文化,將問題=改善機會的理念傳遞給每一位員工。
◆質量管理流程革新實施之前,2019年寧波公牛問題發(fā)現(xiàn)總數(shù)達12333條,根本解數(shù)達1962條,根本解關閉率15.90%。革新實施之后,2020年問題發(fā)現(xiàn)總數(shù)達20436條,同比增長65.7%,同比增長98.78%, 根本解數(shù)達3900條,同比增長98.78%,根本解關閉率19.08%,同比增長19.96%;
◆2021 年問題發(fā)現(xiàn)總數(shù)達33268條,同比增長62.79%,根本解數(shù)達9523條,同比增長144.18%,根本解關閉率28.63%,同比增長50%;
◆22年截至8月份,問題發(fā)現(xiàn)總數(shù)達23053條,根本解關閉數(shù)7664條,根本解關閉率33.25%,預計全年可發(fā)現(xiàn)問題34580條,同比增長3.94%,可關閉根本解數(shù)11496條,同比增長20.72%,根本解關閉率33.25%,同比增長16.14%。外部質量根本解關閉率保持在45%以上。
◆質量流程革新三年以來,截止22年8月份,較19年相比,問題發(fā)現(xiàn)數(shù)增長86.92%,根本解數(shù)增長290.62%,根本解關閉率增長108.98%。
◆寧波公牛外部不良率連續(xù)三年降低,至2022年實現(xiàn)154ppm的行業(yè)第一水準,相比2019年,降低76.63%。
根本解流程管理方法與自主質量均屬于行業(yè)革新性創(chuàng)新,在公司內部,產品可靠性指數(shù)(S=丨X1-X2 丨/2μ;X1、X2代表性能的最高值與最低值,μ代表總體性能均值)從0.93(等級低)提升至0.26(等級高)。在公司外部,作為行業(yè)領頭羊,帶領同行業(yè)共同進步,為客戶提供又好又便宜的產品,逐漸淘汰掉社會上的殘次品,為客戶創(chuàng)造一個安全舒適可信賴的用電環(huán)境。
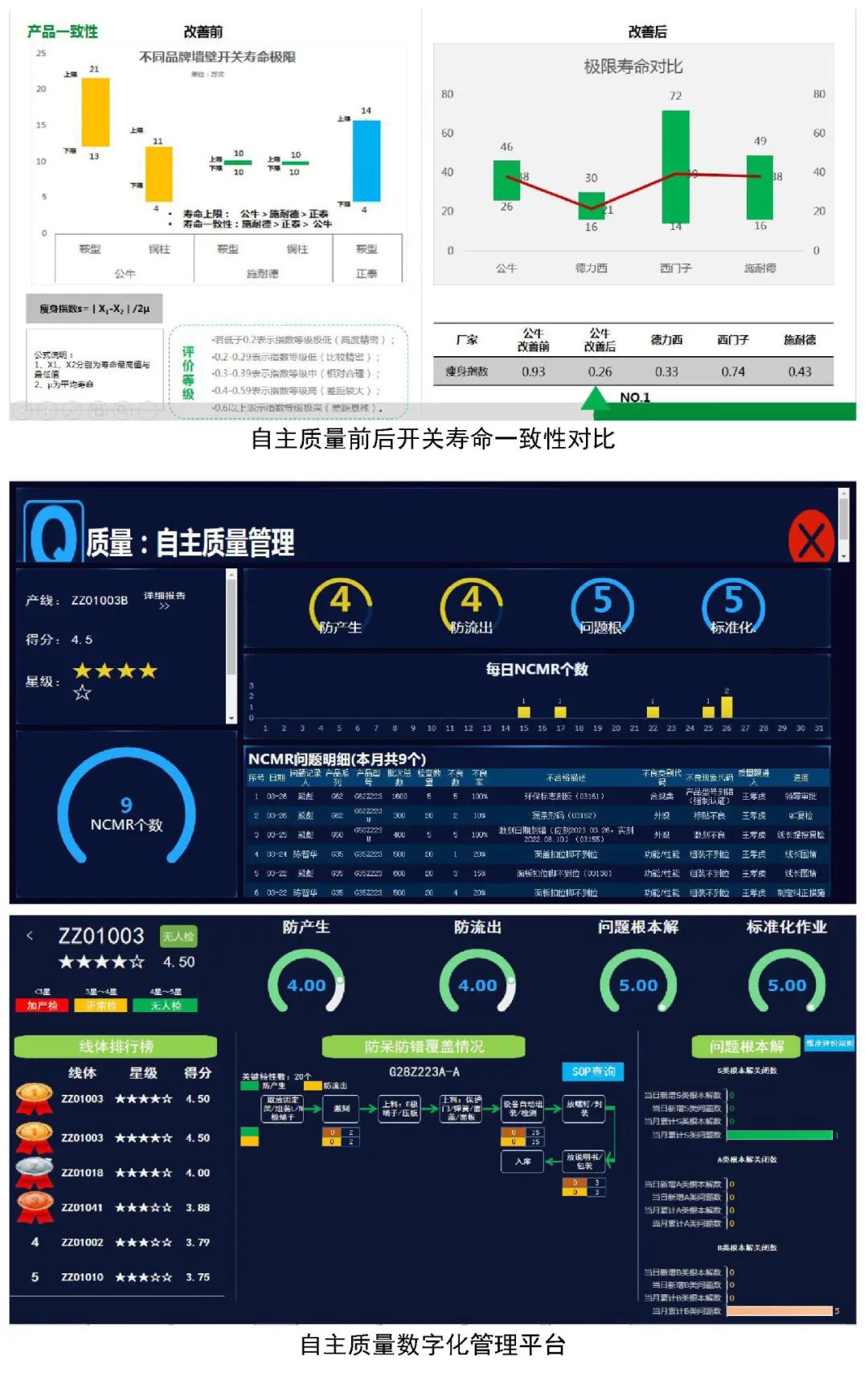
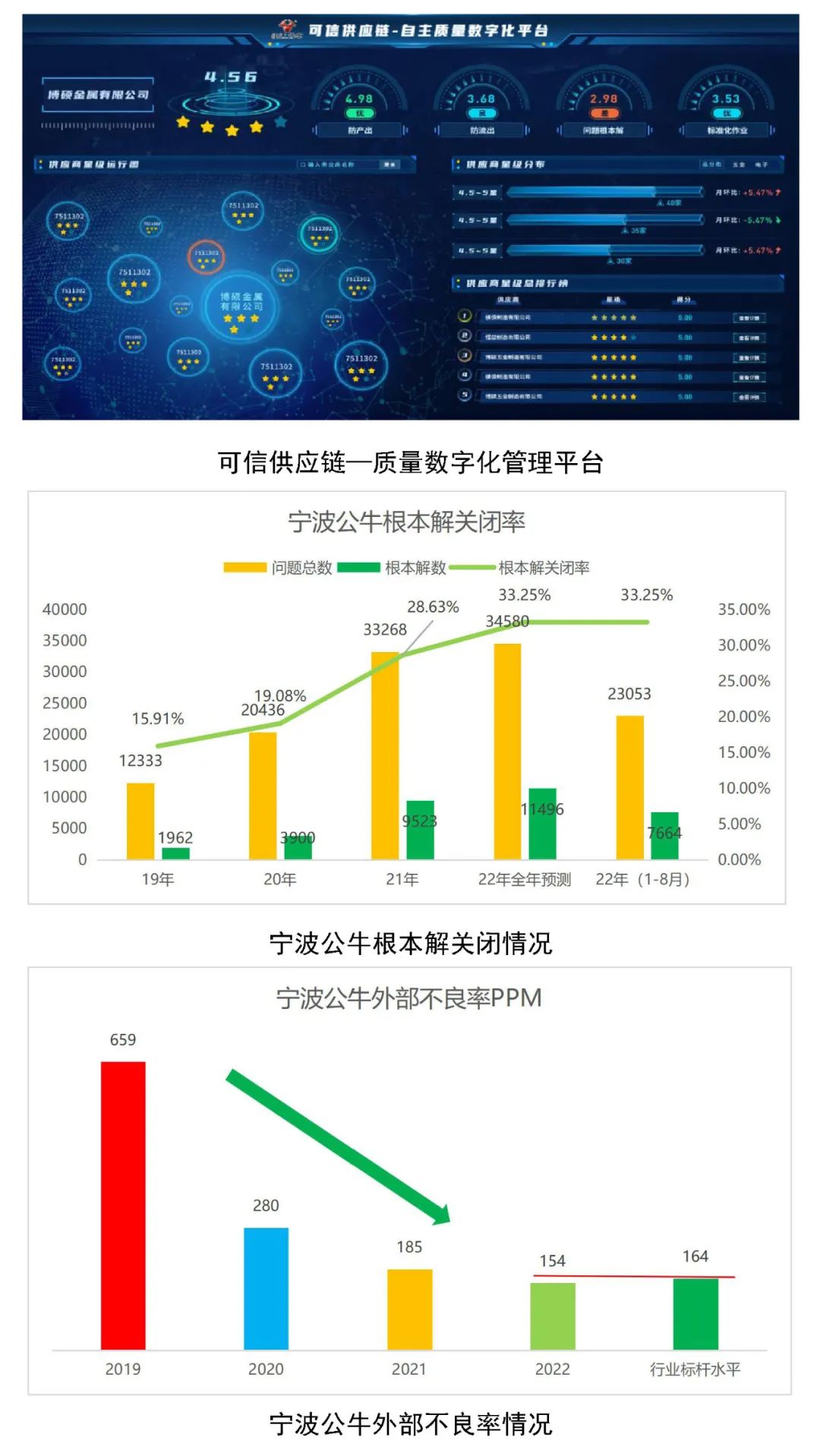
可推廣、可共享性:項目擁有清晰的框架邏輯與標準規(guī)則,在行業(yè)內屬于首創(chuàng),具備一定的推廣前景,目前在寧波公牛孵化打基礎,且已在集團內部推廣。實現(xiàn)標桿線覆蓋率50%,關鍵供應商覆蓋率30%,質量外部客退率降低76.6%。
質量根本解流程管理方法不同于傳統(tǒng)的問題解決方法,規(guī)定了根本解的四大措施:“優(yōu)化設計”“升級設計標準”“優(yōu)化工藝—增加防呆”“優(yōu)化工藝—增加100%自動測試”。標準簡單明晰,易于理解,具備可推廣性,在公牛內部,從寧波公牛電器有限公司生根發(fā)芽,已推廣至轉換器、生活電器、智能門鎖等其他8個事業(yè)部,幫助老事業(yè)部煥發(fā)新生,新事業(yè)部快速發(fā)展。
在公牛集團外部,已將此方法論推廣至26家供應商應商,助力供應商根本解關閉率從24.6%提升至45.47%。